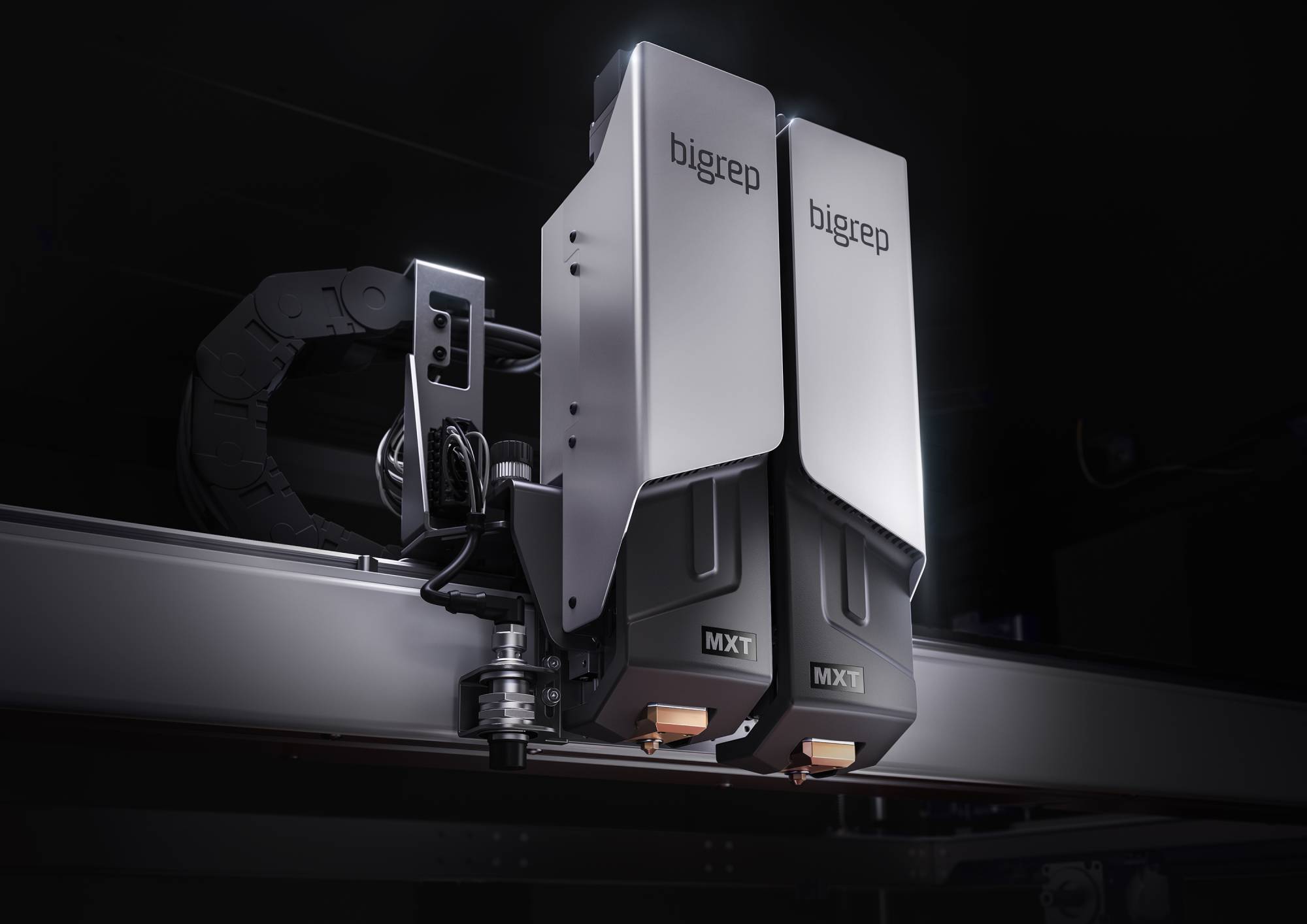
BigRep MXT
Drucken in neuer Geschwindigkeit
MXT steht für Metering Extruder Technology und wird von BigRep eigens entwickelt. Sie soll in den BigRep-den PRO- und EDGE-Druckern eingesetzt werden.
Die MXT-Technologie ermöglicht bei höchster Einstellung eine fünfmal höhere durchschnittliche Extrusionsrate als ein durchschnittlicher FFF/FDM-Drucker. Mittels MXT soll eine vollständige Kontrolle über die Extrusionsgeschwindigkeit und die Menge des extrudierten Materials errreicht werden.
Die Drucker werden mit dem Bewegungssystem von Bosch Rexroth ausgestattet sein, was ihnen einen großen Vorsprung bei Druckgeschwindigkeit, Präzision und Qualität verschafft. Sie sind außerdem mit IoT-Konnektivität ausgestattet, sodass Benutzer sie problemlos in ihre Smart-Factory-Abläufe integrieren können.
Projekt
BigRep GmbH
Tätigkeiten
Konzeptdesign
Produktdesign
Art Direction
Software
Solidworks
Adobe Suite
KeyShot
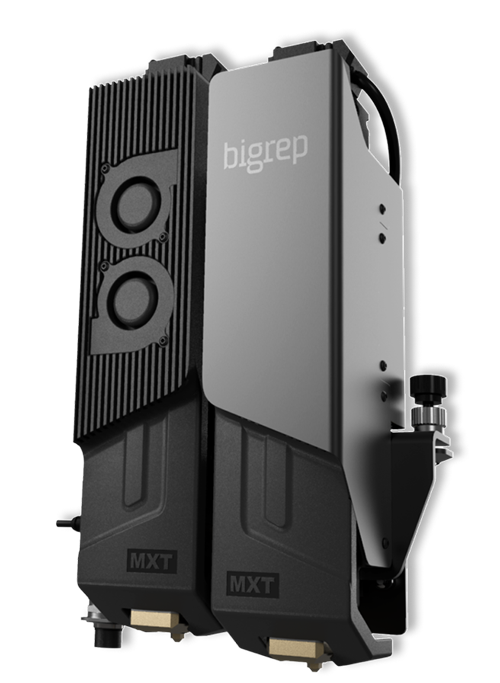
Das Projekt
Der MXT-Extruder basiert auf einer neu entwickelten Technologie, die deutlich leistungsfähiger ist als bisherige Extruder.
Dies sollte sich auch im Design des Extruders widerspiegeln, wobei die Einhausung nicht nur einen rein ästhetischen Zweck erfüllen sollte; vielmehr hat sie auch noch die Funktion, den Extruder und das extrudierte Material zu kühlen.
Die Abdeckung des Extruders besteht aus Edelstahlblechen und einem 3D-gedruckten Bauteil. Dieses gedruckte Bauteil enthält Luftkanäle, die das extrudierte Material an der Düse kühlen sollen. Die Luft hierfür wird von einem Ventilator an der Oberseite durch die Kanäle gedrückt.
Der Aufbau eines modularen Systems ermöglicht den einfachen Wechsel und Test unterschiedlicher Kühldüsen und Geometrien.
Die Herausforderung
Das Projekt war auf technischer als auch gestalterischer Seite sehr reizvoll und herausfordernd. Die Entwicklung der Umhausung fand parallel zur technischen Entwicklung des Extruders statt. dies erforderte eine enge Verzahnung mit Abteilungen aus dem gesamten Unternehmen wie Maschinenbau, Elektrotechnik und Testing.
Die von mir entwickelte innovative Art der Luftführung wurde letztendlich auch patentiert.
Der Entwurf
Die Arbeit am Extruder war von vielen Entwicklungsschleifen zwischen Entwurf, Prototyping und Testing geprägt.
Die Umhausung ist eng mit der Funktion und Konstruktion des Extruders verknüpft. Der 2D Entwurf wurde sehr schnell in 3D modelliert, um die Ausarbeitung auf Basis der bestehenden technischen Geometrien vornehmen zu können. Dabei wurden viele verschiedene Varianten ausprobiert und die Ergebnisse aus den Testings in den Entwürfen umgesetzt.
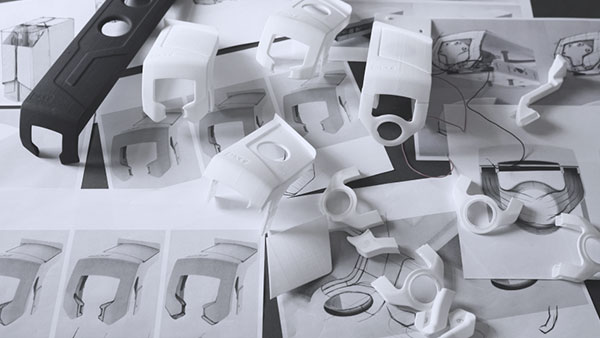
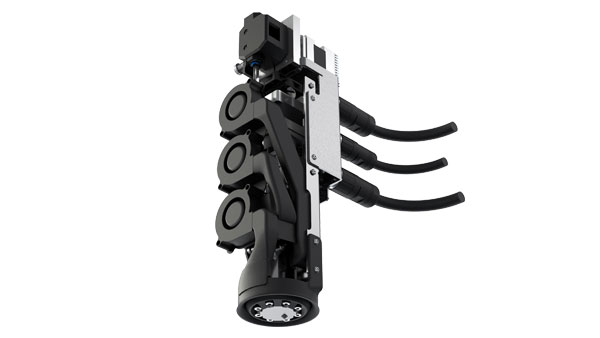
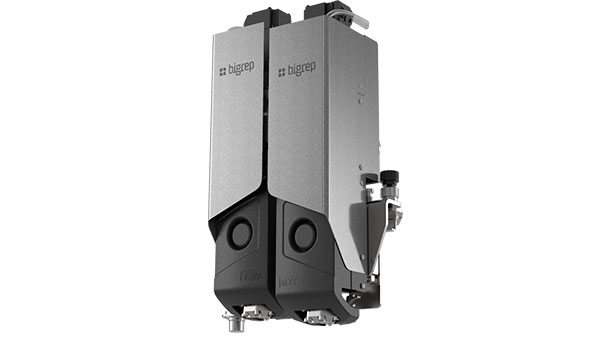
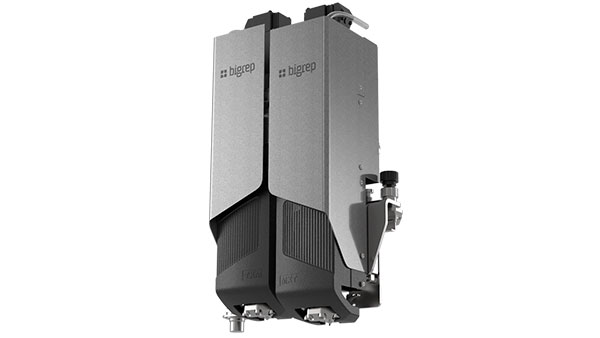
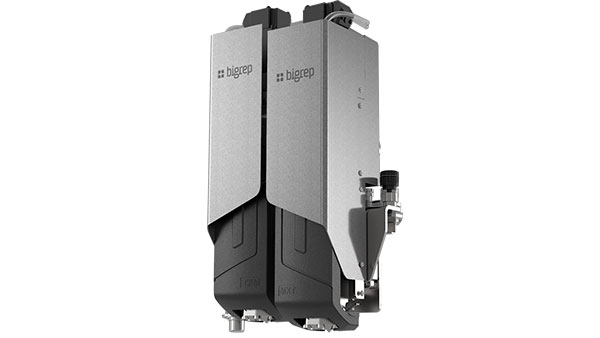
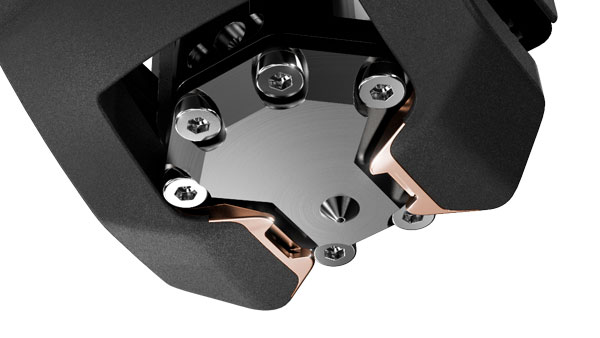
Das technische Konzept
Das Hauptaugenmerk lag auf dem 3D-Druckteil, welches sowohl die Kühlung von Extrudern als auch die des extrudierten Materials bereitstellen sollte. Diese sollte in zwei getrennten Luftkreisläufen stattfinden. Um verschiedenste Varianten in der Luftführung testen zu können, entwarf ich ein modulares System, anhand dessen sehr schnell viele verschiedene Geometrien getestet werden konnten.
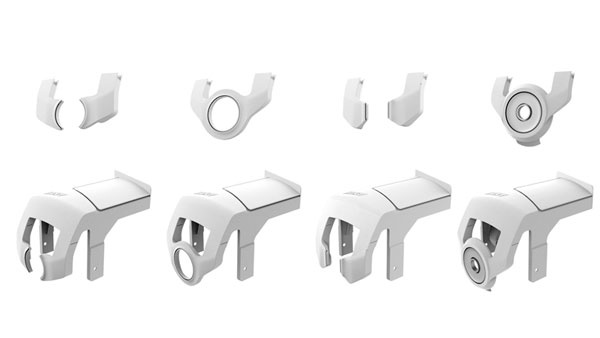
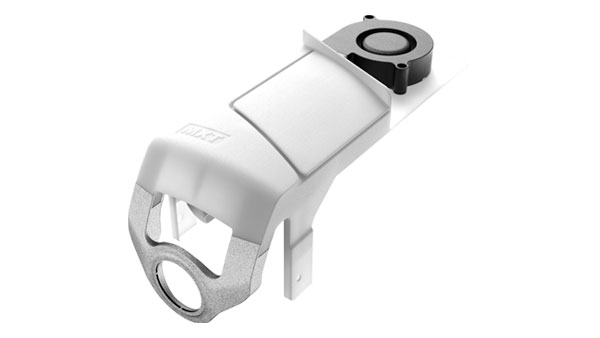
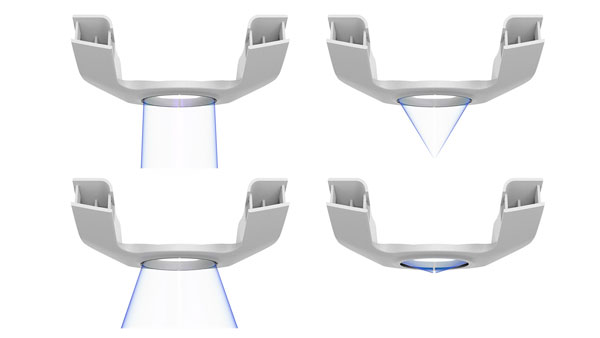

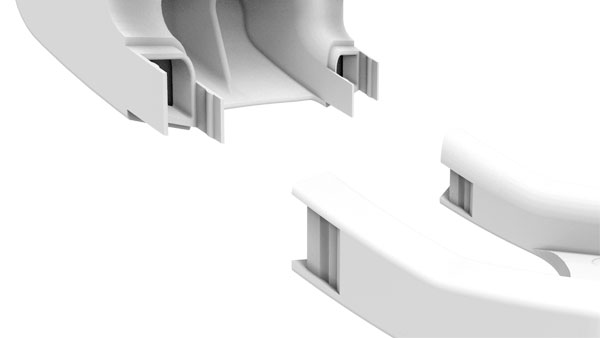
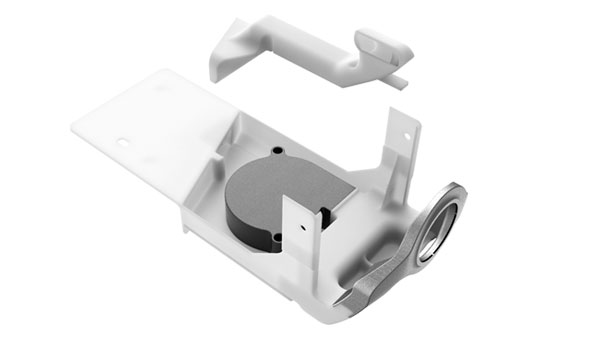
Prototyping & Testing
Das Prototyping sowie das finale Produkt werden mittels 3D-Druck hergestellt.
Dabei war zu beachten, dass das verwendete thermoplastische Material mit einem relativ niedrigen Schmelzpunkt teilweise nur wenige Millimeter von sehr heißen Bauteilen entfernt liegt.
Durch intensives Testing und eine ausgeklügelte Luftführung konnte eine gleichbleibende Stabilität des Bauteils auch neben großer Hitzeeinwirkung gewährleistet werden.
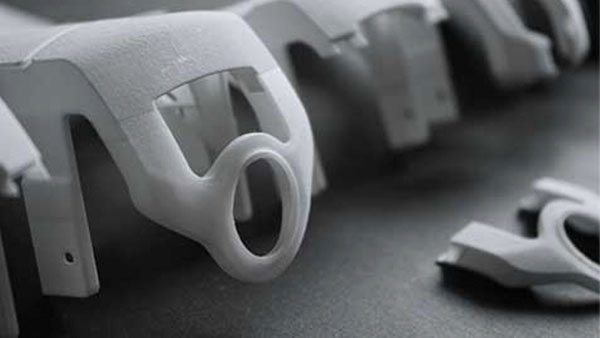
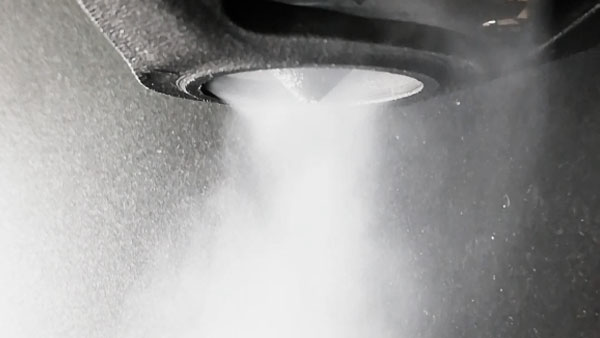
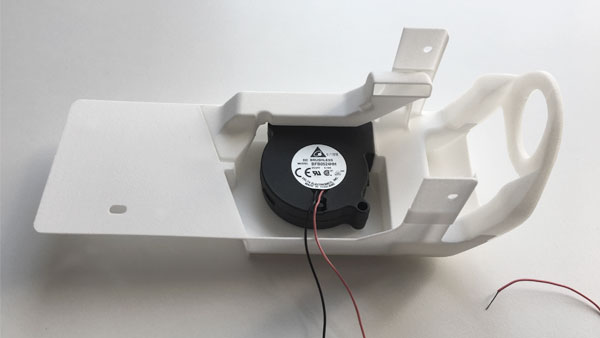
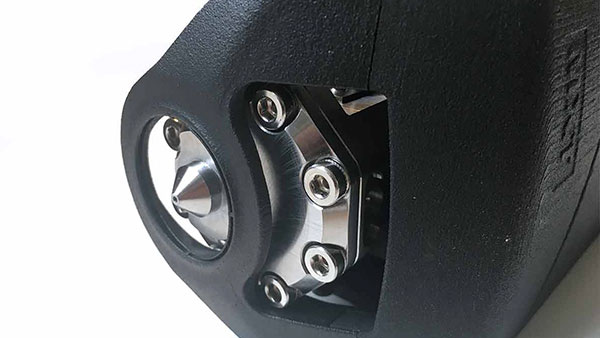
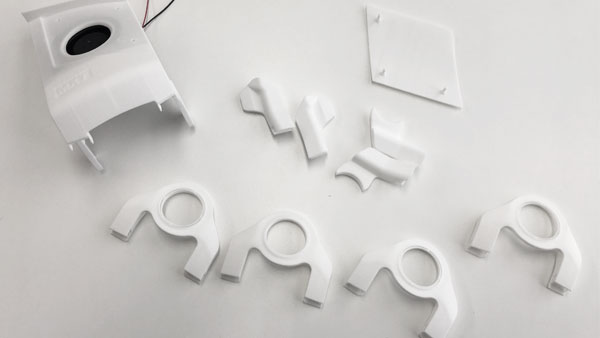
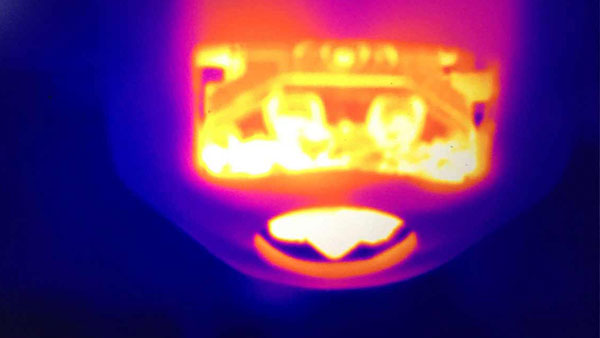